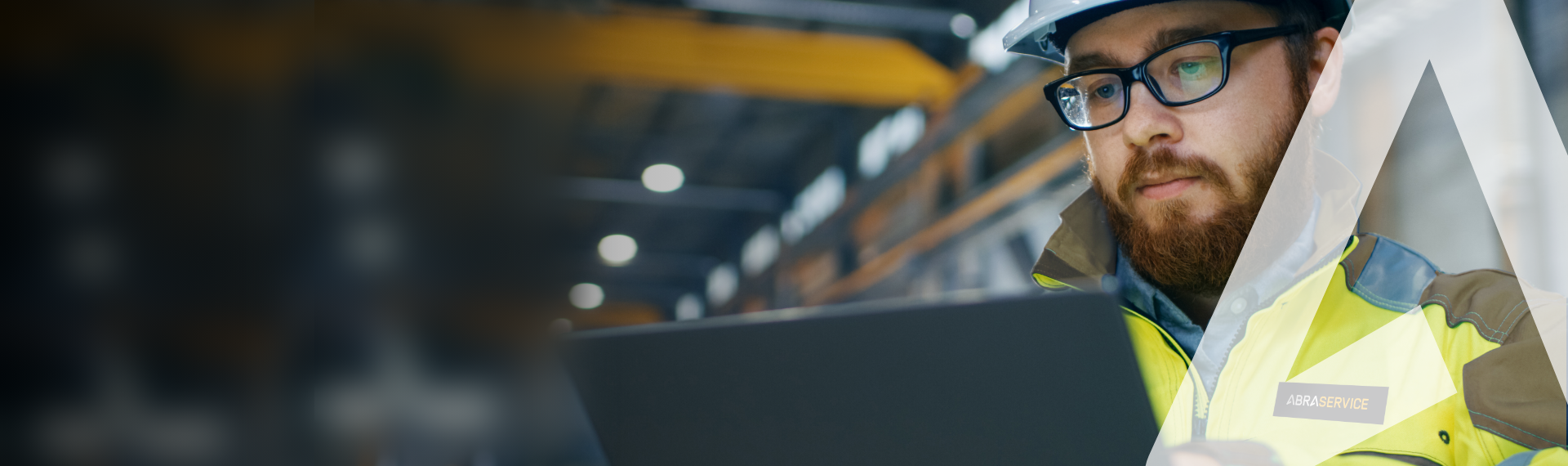
Our services – Solutions made for you
Abraservice has expertise along every step of the solution process - from thoroughly analyzing your requirements to the supply of finished parts ready for fitting. We offer technical support and engineering services whilst keeping an extensive range of materials such as wear-resistant steels, high strength steels, weathering steel, engineering and tool steel as well as tubes and bars.